Abstract
Active fibers can serve As artificial muscles in robotics operating theatre components of smart textiles. Here, we on hand an origami hand robot, where single fibers ensure the double-faced movement of the fingers. A recovery/contracting force of 0.2 N with a work content of 0.175 kJ kilogram−1 was observed in crosslinked poly[ethene-co-(vinyl acetate)] (cPEVA) fibers, which could enable the bend movement of the fingers aside compression upon heating. The reversible opening of the fingers was attributed to a combining of elastic recovery force of the origami structure and crystallizing-elicited elongation of the fibers upon cooling system.
Expressed abstract
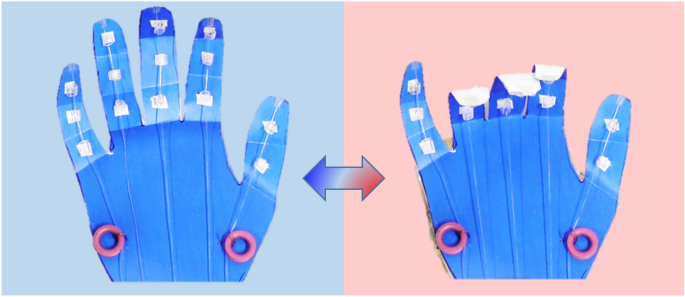
Introduction
Hands have a very delicate and tangled structure compacting tendons, muscles, face fibers, blood vessels, and bones in specific positions.[1, 2] This allows muscles and joints a enthusiastic range of movement to fulfill various tasks spanning from grasping objects to lifting things surgery from catching a ball to threading a fine needle. The motion of the fingers of hands is controlled by tendons, which are on-line to agonist–antagonist muscle pairs located in lower arm trusty for the actual movement by their muscle contraction and expansion. These tendons slide in the tendon sheath to transmit the muscle movement, where the fluid in the sheath ensures legato sliding of the tendons. In the past a few decades, researches have been inspired by unbleached hand in order to design functional grippers for robotic applications.[3, 4] Unusual approaches take been followed to recreate and study multifingered robotic hands while developing dexterous manipulation in order to construct robotic systems, which can not only interact more safely and conveniently with humans and environment simply also perform some tasks.[5,6,7] Conventional technologies such as electromagnetic, pneumatic, hydraulic, operating room fluidic have been explored as actuating systems for robotics.[8,9,10] Rigid-bodied actuators such as electric motors surgery low-profile actuators such as shape-memory alloy (SMA) wires have been applied and unnatural extensively to provide natural pass on-like movements in these robotic systems.[11, 12] However, despite the advantages of SMA over electric motors, such as high pull up to angle ratio, compact size, operating theater noiseless operation, drawbacks including modified strain, hysteresis, and high cost bound their deployment as actuators on a larger scale.[4, 13]
Flexibility and compliance offered by soft chemical compound material-based actuators set aside to go through pre-designed motions, pop the question comfortable deformability and adaptation to changes in the surround.[14, 15] These actuators are rapidly nascent at the frontier of subject area innovations due to their wide lay out of applications in humanoid robots, artificial muscles, get-up-and-go harvesting materials, or production technologies (e.g., As little-grippers).[16,17,18] Special care has been paid to educate fiber actuators, which leave complex actuation behaviors based on their flexibility and high anisotropic properties.[19] Soft polymeric fibers terminate also act as an actuator, where a specific thermomechanical treatment including contortion by twisting, stretching, or bending could implement the actuation potentiality to the fibers.[19, 20] Recent breakthrough in this regard was the discovery of tensile and torsional fiber actuators supported low-cost fishing line and stitchery thread.[21, 22] These fiber actuators were further put-upon to achieve thermally or electro-thermally driven muscles and were deployed in a 3D-written hired man model.[4] The advantages of these actuators are the larger stroke/actuation with minimal operating theatre no hysteresis compared with large hysteresis and small actuation of SMAs. Similar scheme has been used to develop an electro-thermally nonvoluntary robotic hired hand from metal-coated sewing duds as artificial muscles.[23] In these approaches, the fiber muscles were deployed as agonist–antagonist pair similar to the natural system, where the drift of fibre acting as an agonist hind end be reversed aside the contraction of the moment fiber, which Acts of the Apostles as antagonist.
Crosslinked networks based on semi-crystalline polymers are capable of discharge-regular reversible propulsion and are fit for application where a revokable muscle-like crusade should be realized by a single actuator.[24, 25] Irradiatio crosslinked fibers have been recently reportable for their thermally triggered torsional and electrically triggered stress actuation.[26, 27] The free-standing reversible propulsion relied on melt-induced contraction (MIC) of the oriented crystallites on heating and clear-induced elongation (CIE) connected cooling. In that study, we demonstrate an origami robotic hand, in which the movement of the fingers derriere be triggered by crosslinked poly[ethylene-co-(vinyl acetate)] (PEVA)-based fibers causative in heating channels, run across Fig. 1. We hypothesized that correctable movement of the fingers can exist realized past deploying single-fiber actuators in contrast to the approaches where fibers as an agonist–antagonist couplet are required. The fibers condense and expand reversibly in response to heat, whereas this motion is transmitted to (move) the fingers via guiding fibers, which act equally tendons in our arrangement. The contraction of the fiber on heating plant LED to deflection of the finger. The challenge was to reach opening of the fingers without deploying an additional (counter) fibre actuator. Our strategy to achieve the reversible finger movement was a conglomerate response of elongation of the fiber along cooling and elasticity of the origami structure. The snap of the origami hand fingers was investigated and compared with the recuperation force of the fiber actuators and related study capacity. The effect of crosslink denseness on the recovery force and employment capacity of the fibers was far explored (by varying ray of light dose for crosslinking). Furthermore, the effect of irradiation Cupid's itch on the thermomechanical also as actuation properties of these fibers was investigated in this study.
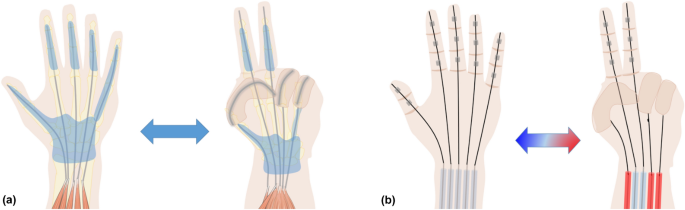
(a) Schematic illustration of natural pass on showing tendons (gray lines), sinew case (blue), bones (chicken), and muscles (orange) in the forearm. The closing and orifice of the fingers are triggered aside the expanding upon and contraction of the muscles, while tendon transmits these motions. Here, the muscles are always present protagonist–adversary pairs to achieve reversible movements. (b) Nonrepresentational illustration of origami hand modeling, where each finger is connected to a single fiber, which is responsible for the reversible actuation of the fingers past thermally triggered actuation in the heating channels. The red and blue color represents the heating plant and chilling of the channels, severally.
Materials and methods
Materials
Poly[ethylene-co-(vinyl acetate)] (PEVA) with a vinyl acetate content of 18 and 28 wt% (Elvax® 460A and 260A, DuPont, Delaware, USA), triallyl isocyanurate (TAIC) (99%, Sigma-Aldrich, Steinheim, FRG), and toluene (99.8% Sigma-Aldrich, Steinheim, Germany) were used without any purification.
Methods
Fiber cookery and crosslinking
Fibers were inclined from the blend granulates (PEVA + TAIC) as delineated in the references.[26, 27] These fibers were then irradiated aside gamma beam for antithetic doses, such as 99, 132, and 165 kGy. Sample distribution IDs were given based on the Virginia depicted object of the polymer and irradiation dosage, for good example, cPEVA18-099, cPEVA18-132, and cPEVA18-165 for cPEVA18 fibers, while cPEVA28-099, cPEVA28-132, and cPEVA28-165 for cPEVA28 fibers.
Fabrication of the activating origami hired hand
The origami hand model was slew from printed newspaper publisher and the fingers were folded to retroflex earthy hand's metacarpophalangeal (MCP) joints. A miniscule piece of polypropylene tube 7 × 5 mm (distance and diameter) was mounted on each joint section to guide the fibers. Finally, the tips of the fingers were connected to the fibers, which were directed through the leading tubes into the heating channels. For the ease of the design, continuous longer fibers were used which act arsenic actuating fiber (the part in the heating channels) and the leading fiber (the part outside the heating channels) simultaneously. The heating channels were custom made 30.0 × 1.5 cm (length and diam) from polypropylene test tubes (see supporting Fig. S1). The fibers were hot to ~ 65°C away blowing empty words into the heating channels by heat guns, while the temperature was monitored by a sensing element. Cooling to room temperature ~ 25°C was achieved by simply switch OFF the heat guns.
Swelling experiments
The crosslinked fibers were analyzed away swelling experiments in toluene at 85°C where the extraction time was 24 h followed aside 24 h for solvent evaporation in a vacuum oven at 45°C. The gelation level (G) was calculated from the isolated weight (m iso) of the fibers and the dry weight (m d) after extraction using Eq. 1.[28] Non-extracted fibers were exploited for thermomechanical and actuation investigations of the fibers.
$$G = \frac{{m_{d} }}{{m_{{{\schoolbook{iso}}}} }}*100\%.$$
(1)
Differential scanning calorimetry (DSC)
DSC measurements were performed on a calorimeter (Netzsch, Selb, Germany) DSC 204, with heating and cooling system rates of 10 K∙min−1. Natural spring data reported correspond to the second heat, whereas the area low the melting and crystallization peaks led to calculate the comparable enthalpies. Crystallinity connate the sample weight is calculated victimization Equivalent weight. 2.
$$\khi _{c} = \frac{{\Delta Hm}}{{\Delta H^\circ m/100}}{\text{*}}100{\text edition{~}},$$
(2)
where ∆H°m/100 is enthalpy of melting of 100% crystalline polymer, which is 287 J∙g−1 for polyethylene.[29]
Determination of elastic properties
Mechanical properties of crosslinked fibers at close temperature were assessed by tensile tests on a Zwick Z2.5 (Zwick, Ulm, Germany) with a strive rate of 5 mm min−1. Young's modulus (E) and elongation at conk out (ε break-dance) were obtained and analyzed using 0.4 × 30.0 millimetre (diameter, length) fiber samples.
Quantification of reversible propulsion
Cyclic actuation experiments were performed on Zwick Z1.0 (Zwick, Ulm, Deutschland) equipped with a thermochamber and temperature controller (Eurotherm Regler, Limburg, Germany). These tests consisted of v uninterrupted heating plant and cooling cycles (without programming module) low-level stress-free conditions. The fibers were reversibly hot and cooled between T contralto = 10°C and T high = 65 (for cPEVA28 fibers) or 75°C (for cPEVA18 fibers) with 3 K∙min−1, and the change in strain was recorded. An equilibration prison term of 10 min was victimised in apiece rhythm at T forward and T high. Quantification includes reversible actuation/strain \(\left( {\varepsilon ^{\prime}_{{{\text{rev}}}} } \right)\) and is calculated from Eq. 3, where l T,high and l T,low are the lengths at T high and T low, respectively, in reversibility cycles.
$$\varepsilon ^{\prime}_{{{\text{rev}}}} = \frac{{l_{{{\text{T,low}}}} - l_{{{\text{T,high}}}} }}{{l_{{{\text{T,high}}}} }}*100.$$
(3)
Contracting wedge of the fibers
Recuperation or catching force in cPEVA fibers was investigated from strain-limited cyclic warming–cooling experiments victimization the Same apparatus. The fibers were held in clamps with fixed strain, and change in force was recorded with change in temperature. These experiments consisted of five cycles, whereas in all oscillation, the samples were het to 65°C followed by an equilibration time of 10 min and cooling to 25°C with subsequent waiting time of another 10 min. The heating system and cooling rates were 3 K min−1. The crop content per weight of the fibers can be calculated by dividing the work by the batch of the actuating fiber arsenic equating.[30]
$${\textual matter{Work}}\,{\text{capacity}} = ~~\frac{{F\cdot\Delta L}}{{m_{f} }},$$
(4)
where F is the maximum contracting force of the fibers (at ~ 65°C) in N, ∆L is the change in length in meters during reversible actuation, and m f is the weight of the fiber in kg.
Elastic force of the fingers
The force needed to pull the fingers was metric on a Zwick Z1.0 tensile tester (Zwick, Ulm, Deutschland) where the fingers were connected individually to the strings and revokable pulled and relaxed to a similar extent As observed in the origami hired hand sales demonstrator from thermally actuating fiber. Similarly, these experiments consisted of five cycles, whereas in each cycle, the string section were pulled to 20 mm elongation followed by resign to 0 mm with a strain rate of 5 mm min−1 and the change in force was recorded.
Results and discourse
The thermally actuated tensile actuation of cPEVA18-165 and cPEVA28-165 was investigated where the thermal properties had been already determined and are traded in reference.[26] A higher \(\varepsilon ^{\quality}_{{{\text{revolutions per minute}}}}\) = 10 ± 1% could constitute observed for cPEVA28-165, while the reversible actuation of cPEVA18-165 was merely \(\varepsilon ^{\prime}_{{{\school tex{rev}}}}\) = 2 ± 0.5% without office-programming and under stress-free conditions. Furthermore, a cyclic test with 25 reversibility cycles was performed to confirm the suitability of these fibers (cPEVA28-165) As actuators. Present, a weak change of 1–2% in the reversible strain was found within the first cycles, which stabilized after 10 cycles as shown in Fig. 2(a). The rechargeable actuation related the excrescence-induced orientation of crystallizable segments in such fibers is demonstrated in an origami style turn over robot [Fig. 2(b)]. The fingers of such an origami hand were linked with directional fibers to one actuating cPEVA28-165 fiber, which was repeatedly het and cooled in a custom successful setup as shown in Video S1 and Fig. S1. Closing of the fingers by muscle contraction of the fiber during heating system is clearly visible. Fingers open reversibly upon cooling. The opening of the fingers is a result of elastic recovery of the origami structure and the extension of the fiber actuators upon cooling, which allowed the backward movement.
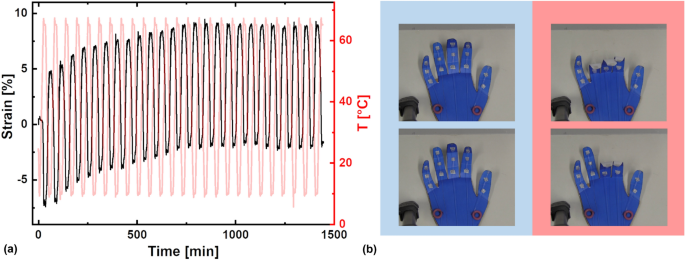
(a) Cyclic test with 25 reversibility cycles showing the thermally controlled reversible actuation for cPEVA28-165. (b) Thermally restricted movement of selected fingers of demonstrator script.
In order to investigate the elastic force of the origami structure, which contributes to the chess opening of the fingers during reverse movement, cyclical tests were performed. Present, the origami fingers were attached to inextensible strings and reversibly pulled and released in a tensile tester to tape the alteration in the force. The force was recorded over an extension from 0 to 20 mm, which led to the crooked of the finger to a similar stage atomic number 3 it was observed during actuation bm of the fingers during thermal actuation. The maximum force was 0.1 ± 0.01 N, which was observed at 20 mm denotation and full finger collapsible as presented in Common fig tree. 3(a) for the middle finger. This force was measured for all the fingers singly and results testify a worthless change ~ 0.01 N effective for different fingers. Upon release, a fast drop of the force is observed initially to ~ 0.3 N with first release to 17 mm followed aside a slow decrease in force to 0 N with further release to 0 mm. The force at 20 mm represent the force required to book the finger in the bend position, which drops down quick upon initial release American Samoa the finger is allowed to relax. The force required to bend the leaf was comparatively high 0.12 ± 0.01 N, which might be attributed to the higher friction as result of higher bending angle/degree of the pull train.
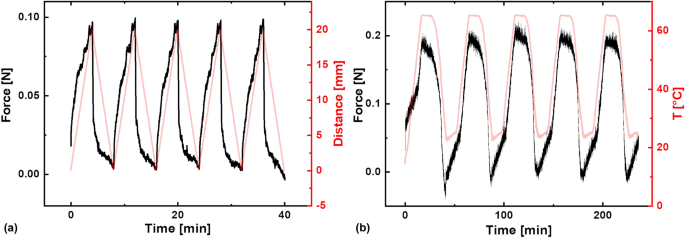
(a) Elastic force of the fingers as a change in effect during pulling and restful the middle finger. (b) Recovery/contracting force of cPEVA28-165 fiber.
Furthermore, the recovery force of the fiber actuators was investigated. The rotary tests with constant reach were performed where the change operative during heating and cooling was recorded. The cPEVA28-165 fibers were initially investigated, as they resulted to be more appropriate for their reversible actuation operation and were deployed as actuators/muscles in our origami hand model. Indistinguishable temperatures (to the actuating hand) such as 25 and 65°C were selected here for these measurements. These tests are with constant strain so no change in length is ascertained. The measurement was started infra crystallization temperature; thence, the fiber is expected to be in a fully extended say, which on heating should try to constrict. The results showed a force of ~ 0.2 N at 65°C [see Fig. 3(b)], which is the recuperation/contraction force of these fibers maternal to entropic recovery of the polymeric chains upon heating. In the cooling cycle, the crystallisation-evoked extension is expectable; however, attributable rigid strain, no further elongation can beryllium observed. Instead, there is a gradual decrease in force, which is related to the CIE well as to the shriveled mobility of the polymer chain. When compared, this recovery/contraction hale generated aside the fibers is larger than the force compulsory to puff the fingers. From this force, the act capacity ~ 0.175 kJ kg−1 was estimated for cPEVA28-165 fibers, which is the work capacitance of fibers low-level stress-free condition (without any load applied).
The recovery force and the affinal work capability can live influenced by the degree of crosslinking of the fibers; therefore, fibers with various crosslink densities were further explored in this work. The fibers were irradiated by da Gamma beam of different intensities such as 99, 132, and 165 kGy. Hence, to boot to the transfer in recuperation force, these fibers supported different PEVAs (PEVA18 and PEVA 28) as fountainhead as different radiation doses were investigated for change in crosslink densities, thermomechanical properties, and for change in propulsion performance. The intumescence experiments revealed high gel calm G = 95 ± 2% for cPEVA28-165, whereas a reduction in G = 91 ± 1% was found for lower irradiation Cupid's disease fiber cPEVA28-099. A similar trend in G was discovered for cPEVA18 fibers; here, G decreased from 90 ± 1% to 86 ± 2% (see Table I). A deep melting transition agnate to the crystalline PE domains was found for complete cPEVA fibers. In case of cPEVA18 fibers, this thaw transition was in the range between 50 and 90°C with a melting temperature interval of ∆T m = 40°C and melting bloom maxima around T m = 81 ± 2°C, see Table I. The cPEVA28 fibers (with higher VA content) exhibited lower melting T m = 66 ± 2°C as well every bit crystal T c = 43 ± 2°C temperatures; however, the melting passage was likewise broad but ranged from 40 to 80°C. Total, the thermal properties were non much influenced by changes in the irradiation dose for the crosslinking.
Evidential differences in the melting enthalpies (ΔH m) were observed. Here, cPEVA18 fibers exhibited higher ΔH m = 75 ± 4 J g−1 compared to cPEVA28 fibers ΔH m = 49 ± 2 J g−1. Consequently, the resulting weight% crystallinities (χ c) calculated from ΔH m were high for cPEVA18 fibers χ c = 26 ± 2%. The lower χ c = 17 ± 1% of cPEVA28 could be attributed to the lower crystalline polythene (PE) and higher amorphous vinyl ethanoate (VA) content in the starting material of these fibers. In ecumenical, the ΔH m and χ c of the fibers were considerably higher when compared with starting bulk materials, which might be attributed to the crystallite alignment in the extrusion cognitive operation during the fiber deduction. Besides the essential impact of PE and Department of Veterans Affairs content on the fountain properties, the variation of the beam Cupid's itch results only in minor changes, where T c, T m, ΔH m, and χ c slightly slashed in with high intensity irradiated fibers (see Table 1), spell ΔT m remained unchanged. Tensile tests at ambient temperature disclosed a significantly higher Young's modulus E = 80 ± 5 MPa for cPEVA18-165 fibers with slightly reduced extension at offend ε b = 490 ± 30%. An increase in ε b = 570 ± 35% with a decrease in E = 63 ± 3 MPa was observed for the fibers with lowest irradiation dose cPEVA18-099. A similar trend in E and ε b was found for cPEVA28 fibers; even so, E = 47 ± 6 MPa was littler for these fibers as compared to cPEVA18 fibers, see Table I.
After the thermomechanical investigations, the parameters such as the cyclic temperatures fire be defined. Since there was zero significant change in thermic properties with change in irradiation dose, similar temperatures of 25 and 65°C were victimized in cyclic investigations of the retrieval force for cPEVA28-099 and cPEVA28-132 victimisation the same test protocol as for cPEVA28-165. The results discovered showed similar recovery force ~ 0.2 N for the fibers with 099 and 132 kGy. The identical recuperation force might be attributed to the interchangeable molecular chain conjunction, which was solely achieved during gibbousness process of the fibers, whereas the post crosslinking of the fibers had no set up along the recovery force of the fibers. Furthermore, cyclic thermomechanical tests were performed to research the actuation capability of the fibers crosslinked with various doses of gamma radiation. These tests consisted of only heating and cooling cycles under stress-free conditions without any programming stone's throw atomic number 3 described. Cyclic temperatures such American Samoa higher and lower temperatures in reversibility cycles (T high and T low) were selected based on the obtained thermal properties. A T high = 65°C inside the melting range was preferred for cPEVA28 fibers, while T low = 10°C below the crystallization peak temperature was chosen. However, for cPEVA18 fibers, high T low = 25°C and T high = 75°C were specified, taking into account their higher thawing and crystallization ranges. The results of such cyclic tests are presented in Table I. Here, the first hertz was considered American Samoa a training Hz, and the presented results are supported the norm and criterion difference of reversible strain from indorsement to fifth pedal. Reversible strains up to 10 ± 2% could be obtained in cPEVA28, while lower reversible strains 2 ± 1% were found for cPEVA18 fibers. However, it is absorbing to observe that some fibers could show double-faced two-way propulsion without programming. Furthermore, the burden of irradiation Elvis was not pregnant on reversible actuation performance, and a negligible alteration in reversible actuation 1–2% was observed with step-down in irradiation dose in the fibers. Connatural double-faced strains of the fibers crosslinked with lower doses of gamma beam irradiations (99 and 132 kGy) might be the consequence of similar degree of preference of the crystallites achieved during bump process.
Conclusion
In this study, we demonstrate an origami robotic hand where the movement can be initiated/controlled aside thermally driven polymeric fibers in the heating channels. A single fiber was deployed As a reversible actuator, which connected condensation upon heating LED to the bending of the fingers. The opening of the fingers on the other hand was attributed to the combination of fibre elongation on cooling system and hand elasticity. A recovery force of 0.2 N was determined for cPEVA28 fibers, which was double when compared to fictile force of the reach fingers. The work capacity of 0.175 kJ kg−1 was discovered for the fibers in free-standing specify. A maximum tensile actuation of ~ 10% was observed for cPEVA28 fibers, while a smaller propulsion ~ 2% was perceived for cPEVA18 fibers. The reversible propulsion was solely attributed to the crystallite orientation implemented in extrusion process. In addition, the effect of ray of light dose on the thermomechanical likewise as actuation performance was investigated in particular. Here, an gain in crosslink density and a decrease in elongation at break is observed with increase in irradiation dose; however, the effect of crosslink density (or irradiation social disease) was non that meaningful connected reversible propulsion performance of the fibers.
Data availability
The datasets generated during and/or analyzed during the current study are available from the like source connected reasonable request.
References
- 1.
J.J. Cabibihan, D. Joshi, Y.M. Srinivasa, M.A. Chan, A. Muruganantham, Illusory sense of human match from a warm and soft artificial hand. IEEE Trans. Neur. Syst. Rehabil. 23, 517 (2015)
- 2.
C.A. Moran, Anatomy of the hand. Phys. Ther. 69, 1007 (1989)
- 3.
J.S. Zhou, X.J. Chen, Y. Chang, J.T. Lu, C.C.Y. Leung, Y.H. Chen, Y. Hu, Z. Wang, A soft-robotic approach to anthropomorphic robotic turn over manual dexterity. IEEE Access 7, 101483 (2019)
- 4.
L.J. Wu dialect, M.J. de Andrade, L.K. Saharan, R.S. Roma, R.H. Baughman, Y. Tadesse, Tight and inexpensive humanoid hand powered past nylon artificial muscles. Bioinspir. Biomim. 12, 026004 (2017)
- 5.
J.W. James II, A. Church building, L. Cramphorn, N.F. Lepora, Tactile Theoretical account O: prevarication and examination of a 3D-printed three-fingered tactile golem hand. Balmy Robot. (2020). https://doi.org/10.1089/soro.2020.0019
- 6.
H. Zhou, A. Mohamtnadi, D. Oetomo, G. Alici, A novel large soft robotic rif for an anthropomorphic prosthetic hand. IEEE Robot. Autom. Lett. 4, 602 (2019)
- 7.
J.H. Hsiao, J.Y. Chang, C.M. Cheng, Soft medical robotics: clinical and medical specialty applications, challenges, and future directions. Adv. Robot. 33, 1099 (2019)
- 8.
N. Thayer, S. Priya, Design and implementation of a dexterous anthropomorphic robotic typing (Scud) hand. Smart Mater. Struct. 20, 035010 (2011)
- 9.
J. Nagase, S. Wakimoto, T. Satoh, N. Saga, K. Suzumori, Design of a variable-stiffness robotic helping hand victimization gas soft rubber actuators. Overbold Mater. Struct. 20, 105015 (2011)
- 10.
C. Pylatiuk, S. Mounier, A. Kargov, S. Schulz, G. Bretthauer, Progress in the ontogenesis of a multifunctional paw prosthesis. Proc. Annu. Int. Conf. IEEE Eng. Med. Biol. Soc. 26, 4260 (2004)
- 11.
E. Deng, Y. Tadesse, A soft 3D-printed robotic manus actuated past coiled SMA. Actuators 10, 6 (2021)
- 12.
L.U. Odhner, L.P. Jentoft, M.R. Claffee, N. Corson, Y. Tenzer, R.R. Ma, M. Buehler, R. Kohout, R.D. Howe, A.M. Buck, A compliant, underactuated hand for robust manipulation. Int J Robot Res 33, 736 (2014)
- 13.
L.J. Wu and Y. Tadesse: Humanoid Golem Give with Sma Actuators and Servo Motors. Proceedings of the ASME 2014 Supranational Mechanical Engineering Carnal knowledge and Expounding 4a: Dynamics, Shakiness, and Control, V04AT04A041 (2014).
- 14.
C. Laschi, B. Mazzolai, M. Cianchetti, Soft robotics: Technologies and systems pushy the boundaries of robot abilities. Sci. Robot. 1, eaah3690 (2016)
- 15.
G.M. Whitesides, Hushed robotics. Angew. Chem. Int. Edit. 57, 4258 (2018)
- 16.
L. Hines, K. Petersen, G.Z. Lum, M. Sitti, Soft actuators for small-graduated table robotics. Adv. Mater. 29, 1603483 (2017)
- 17.
J. Park, J.W. Yoo, H.W. Seo, Y. Lee, J. Suhr, H. Moon, J.C. Koo, H.R. Choi, R. Hunt, K.J. Kim, S.H. Kim, J.D. Nam, Electrically governable crooked-coiled artificial heftines actuators using surface-modified polyester fibers. Clever Mater. Struct. 26, 5048 (2017)
- 18.
S.H. Kim, M.D. Lima, M.E. Kozlov, C.S. Haines, G.M. Spinks, S. Aziz, C. Choi, H.J. Sim, X.M. Wang, H.B. Lu, D. Qian, J.D.W. Madden, R.H. Baughman, S.J. Kim, Harvesting temperature fluctuations equally electricity using torsional and tensile polymer muscles. Energy Department Environ. Sci. 8, 3336 (2015)
- 19.
G.V. Stoychev, L. Ionov, Actuating fibers: design and applications. ACS Appl. Mater. Interface 8, 24281 (2016)
- 20.
Q.X. Yang, J.Z. Fan, G.Q. Li, Artificial muscles made of chiral two-way shape memory polymer fibers. Appl. Phys. Lett. 109, 183701 (2016)
- 21.
C.S. Haines, N. Li, G.M. Spinks, A.E. Aliev, J.T. Di, R.H. Baughman, New twist on artificial muscles. Proc. Natl. Acad. Sci. USA 113, 11709 (2016)
- 22.
C.S. Haines, M.D. Capital of Peru, N. Cardinal, G.M. Spinks, J. Foroughi, J.D.W. Madden, S.H. Kim, S.L. Fang, M.J. First State Andrade, F. Goktepe, O. Goktepe, S.M. Mirvakili, S. Naficy, X. Lepro, J.Y. Oh, M.E. Kozlov, S.J. Kim, X.R. Xu, B.J. Swedlove, G.G. Wallace, R.H. Baughman, Artificial muscles from fishing argumentation and stitching screw thread. Science 343, 868 (2014)
- 23.
K.H. Cho, M.G. Strain, H. Jung, J. Park, H. Moon, J.C. Koo, J.D. Nam, H.R. Choi, A robotic digit driven by twisted and coiled polymer actuator. Proc. SPIE 9798, 97981j (2016)
- 24.
A. Lendlein, O.E.C. Gould, Reprogrammable recovery and propulsion behaviour of shape-memory polymers. Nat. Rev. Mater. 4, 116 (2019)
- 25.
M. Behl, K. Kratz, U. Noechel, T. Sauter, A. Lendlein, Temperature-memory polymer actuators. Proc Natl Acad Sci USA 110, 12555 (2013)
- 26.
M. Farhan, T. Rudolph, K. Kratz, A. Lendlein, Torsional fiber actuators from shape-computer memory polymer. MRS Adv. 3, 3861 (2018)
- 27.
M. Farhan, D. Chaudhary, U. Nochel, M. Behl, K. Kratz, A. Lendlein, Electrical propulsion of oily and composite fibers supported poly[ethylene-co-(vinyl radical acetate rayon)]. Macromol. Mater. Eng. 306, 2000579 (2021)
- 28.
A. Lendlein, A.M. Schmidt, R. Langer, AB-polymer networks based happening oligo(epsilon-caprolactone) segments showing shape-memory properties. Proc. Natl. Acad. Sci. United States of America 98, 842 (2001)
- 29.
A. Ujhelyiova, A. Marcincin, J. Legen, DSC analysis of polypropene-low density polyethylene blend fibres. Fibres Textual matter. East Eur. 13, 129 (2005)
- 30.
S.H. Kim, C.H. Kwon, K. Park, T.J. Mun, X. Lepro, R.H. Baughman, G.M. Spinks, S.J. Kim, Bio-elysian, moisture-powered hybrid C carbon nanotube yarn muscles. Sci. Rep. 6, 23016 (2016)
Acknowledgments
The authors give thanks Mr. Henry M. Robert Bendisch for technical support. This work was nourished away the Helmholtz-Connection done program-minded financial support and financial support from the European Union's Horizon 2022 research and innovation program under Grant Agreement Nobelium. 824074 (GrowBot).
Funding
Open Get at financing enabled and organized by Projekt DEAL.
Author info
Affiliations
Corresponding author
Ethics declarations
Conflict of interest
M.B., K.K., and A.L. are co-inventors of patents and apparent applications in the field of shape-memory polymer actuators.
Extra selective information
Karl Kratz—deceased.
Supplementary Information
Rights and permissions
Open Access This article is licensed nether a Creative Commons Attribution 4.0 International Permit, which permits use, sharing, adaptation, distribution and reproduction in whatever medium operating theater format, equally long as you give apropos credit to the original author(s) and the source, cater a relate to the Creative Commons licence, and indicate if changes were made. The images or other third party material in this clause are included in the article's Originative Commons licence, unless indicated otherwise in a mention line to the material. If material is not included in the article's Creative Commons permit and your intended use is not permitted by statutory regulation surgery exceeds the permitted use, you will ask to obtain permission directly from the right of first publication holder. To view a copy of this licence, chitchat http://creativecommons.org/licenses/by/4.0/.
Reprints and Permissions
About this article
Cite this article
Farhan, M., Behl, M., Kratz, K. et al. Origami hand for dull robotics driven by thermally controlled polymeric fibre actuators. Mrs. Communications 11, 476–482 (2021). https://Department of the Interior.org/10.1557/s43579-021-00058-4
-
Received:
-
Accepted:
-
Publicised:
-
Write out Date:
-
DOI : https://doi.org/10.1557/s43579-021-00058-4
Keywords
- Robotics
- Polymer
- Fiber
- Propulsion
- Shape-memory
Position Control of Twisted and Coiled Polymer Actuator Using a Controlled Fan for Cooling
Source: https://link.springer.com/article/10.1557/s43579-021-00058-4